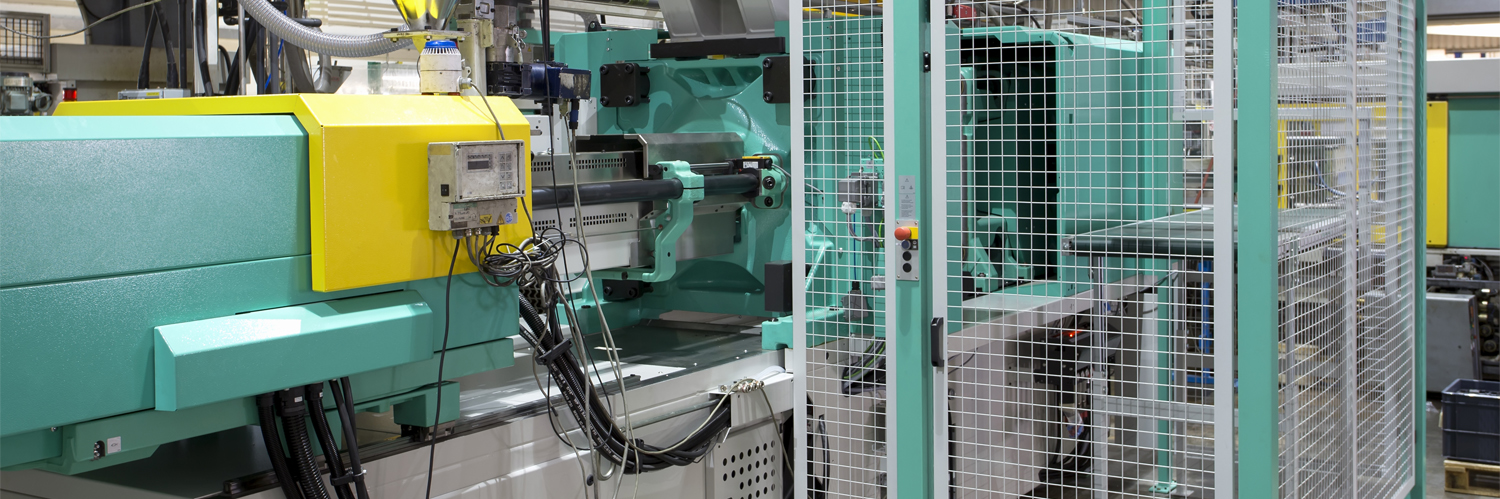
The History of Plastic Injection Mold Making
The manufacturing process of plastic goods has come a long way since the first plastics were synthesized during the industrial revolution. One vitally important part of the process, the production of accurate molds to shape plastics into almost any thinkable form, has also developed and changed considerably.
The Development of Plastic
The word plastic is derived from the Greek word plastikos, which means both “able to be molded” and “pertaining to molding”. Hence, the word was in use long before plastic, as the synthesized material known today, was around. The very word we use to refer to plastic, points back to how capable it is of being molded into various shapes.
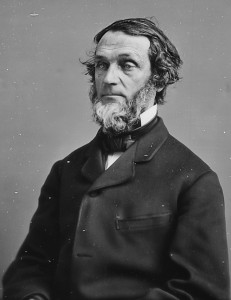
Charles Goodyear’s discovery of the vulcanization to process rubber, greatly helped to further the development of plastics as we know them today. So much so that, four years before Goodyear’s death in 1860, Alexander Parkes had already developed what is considered to be the first man-made plastic, Parkesine. Parkes patented this discovery in 1862.
Parkesine was easy to mold, but unfortunately the material was also highly flammable and expensive to produce.
This discovery – that later developed significantly, and that still continues to develop today – was the first step towards the modernization of molds. Plastic soon became one of the most versatile and easily molded materials available, able to produce an incredibly wide variety of everyday goods.
When the first plastic injection molds were made that could easily mass produce goods, there was an estimated 18,000 materials available for injection molding. Today, the amount of new polymers used for the plastic injection molding process is estimated to expand with approximately 750 new polymers yearly.
The Rise of Plastic Injection Mold Making
In 1872, American inventor, John Wesley Hyatt and his brother Isaiah, patented the first injection mold. It was a very simple machine compared to what would later follow. Working by means of a hypodermic needle and a plunger, which injected plastic through a cylinder into a mold.
Although this invention wasn’t very widely used to mass produce everyday goods, things that had previously been made with materials such as ivory, were now mass-produced by molding plastic. Billiard balls, dice and piano keys were among some the first items that could now be manufactured using this discovery.
German chemists, Arthur Eichengrün and Theodore Becker, further expanded on this discovery . In 1903 they invented the first soluble forms of cellulose acetate. The substance was later made available in a powder that was easy to mold using injection molding processes.
In 1919, Eichengrün went on to develop the first injection molding press. And in 1939 he patented the molding of plasticized cellulose acetate.
Mass Production Through Injection Molding
During World War II, demand for new technologies in various fields, like aviation and transportation, greatly increased. Plastic injection mold making was another field of technology that expanded during this time because of a high demand for inexpensive, mass-produced goods.
American inventor, James Watson Hendry, built the first injection screw machine in 1946. Materials could now be mixed thoroughly before being injected, which enabled Hendry’s invention to mix colored or recycled plastic to virgin materials. Screw injection machines are still in use today, accounting for approximately 95% of plastic injection machines used in modern manufacturing methods.
Hendry later also developed the first gas-assisted injection molding machines in the 1970s. The invention – which allowed for production of hollow, more complex items that cooled quickly – broadened the scope of plastic goods that could be manufactured through injection molding while also ensuring a process that was considerably more efficient on almost every level. Time, cost and waste were all reduced.
Modern Plastic injection mold Making
Plastic injection molds are now made using a highly advanced process, capable of producing molds accurate to a hundredth of a millimeter. This is remarkably precise, as a millimeter is only 0.254 of an inch, meaning plastic molds are now produced accurately within 0.00254 of an inch.
Molds are made from chromium steel, a high durability metal that can withstand repeated high-pressure injection of plastic. Several bars of chromium steel are assembled into a block, called a mold base, and are then mounted on a milling machine to shave the bars to the right dimension.
Strategically positioned holes are drilled in the bases for guide pins and bushings to hold together the two halves of which most molds consist. Following this step, a grinder is used to smooth all the surfaces, preparing the base for the high-precision machining operations necessary to shape it into a mold component.
A computer-guided machine, called a CNC, wears the base slowly to create the mold component’s shape. The CNC machine works at a painstakingly slow pace in order to insure precise accuracy, taking several hours, often more than twenty, to complete a single mold component.
We offer the best Innovative Technology Solutions. Injection molding works best for functional prototyping, pilot runs, bridge tooling and low-volume production of on-demand parts. More than 100 different production-grade thermoplastic, liquid silicone rubber, steel, stainless steel and magnesium materials are available. See our full tool list, we are confident we can help you meet your projects needs with ease.
Download Equipment ListMost mold components, but especially ones with fine detailing, will then go on to a second tooling machine. The second machine, called the EDM, is outfitted with a copper electrode in the shape of the plastic part. The electrode is polished to ensure faultless casting and measured with a highly sophisticated measuring device.
On the EDM, strong electric currents are passed through the electrode to penetrate the mold formed by the CNC machine in the first part of the production process, leaving a cavity, or imprint, shaped like the electrode itself.
The surface of the cavity is polished smoothly to even out any roughness still left after the initial tooling is done.
Very specialized skills are needed to produce plastic molds and, although Plastic injection mold making still remains time-consuming and costly, when the expense is viewed in terms of what is achieved, impeccable part design combined with low-cost mass production of goods, the process is well worth the investment made.
Recent Comments