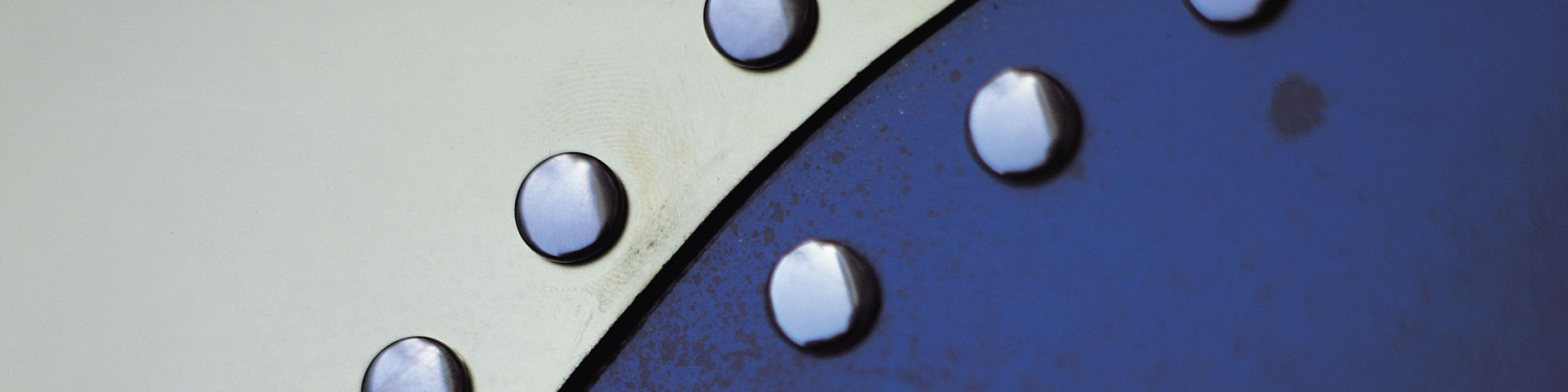
How to Avoid Common Injection Molding Defects
When working with any assembling procedure, various deformities unique to that procedure ordinarily happen. This is true across many processes and industries, including plastic injection molding and high volume injection molding.
There are a few normal infusing forming abandons; be that as it may, an injection molder who is cautious about quality, similar to our group at Quality Mold Shop, will have the capacity to deal with these injection molding deformities, limiting or dispensing with them all together.
These six most common plastic part defects can all be traced to one of three sources: the resin or additives used, the injection molding process, or the mold itself.
Resin and Additive-Caused Defects
Two common defects caused by issues with the resin or resin additives used during injection molding are delamination and discoloration.
Delamination
Delamination, when a completed part has a layer of flaky material at the surface, hurts both aesthetic of your part and its strength. Created by humidity contamination of the resin pellets or by other defilement of the dissolved resin with a different resin, or by discharge specialists in the mold, delamination is the aftereffect of the resin being kept from bonding.
Various strategies, both basic and more mind boggling, can be utilized to counteract delamination. On the off chance that dampness is the issue, pre-drying the resin pellets or expanding mold temperature will offer assistance. In the event that form discharge specialists are the cause, a mold redesign that places more focus on the ejection mechanism will help to eliminate mold release. If it is caused by cross-contaminated resins, that will need to be replaced with virgin material.
Staining
Staining is basically when a completed part is not the same as proposed color. Brought on most usually by extra pellets in the container, excessively hot barrel temperature or remaining resin in the feed zone, the issue can be tended to by altogether flushing the container and bolster zone of a machine in the middle of procedures, subsequently avoiding staining as is normally done. Purging compound can likewise be successful to expel undesirable shading or resin.
Process-Caused Defects
In spite of constant advances in injection molding innovation, process-derived injection molding defects still occur. Two of the most common are burn marks and flow marks.
Burn Marks
Burn imprints are surface imprints, in some cases progressing to debased plastic, that are brought about by either caught air which ends up overheated or genuine resin that overheats. There are three approaches to keep away from burn marks: diminish resin injection speeds, which will bring down the likelihood of air getting caught; include or optimize venting and degassing systems; or reduce the mold and/or melt temperature.
Flow Marks
Flow marks are lined patterns, regularly wavy, or discoloration on a part surface. They are most generally created by resin cooling too rapidly or incorrect gate location. In the most ideal situation, flow marks can be wiped out by expanding injection speed and weight, which will guarantee uniform filling and cooling. In the direst outcome imaginable, a mold upgrade with an accentuation on maintaining a strategic distance from sudden stream heading changes and entryway area might be vital.
Mold-Caused Defects
Flash and short shots are two of the more typical injection molding imperfections brought on by mold outline or upkeep issues.
Flash
Sometimes known as burrs, flash is the occurrence of thin, wafer-like protrusions on a finished part caused when melted resin escapes the mold cavity. Most common along the parting line or up an ejector pin, flash can be caused by excessive injection speed or pressure, in which case the fix is a simple reduction. More often flash is due to poorly designed or severely degraded molds, in which case a redesign or retooling is required. Flash can also be caused by too high of a mold temperature and excessive barrel heat.
Short Shot
A short shot is when a dose of resin misses the mark regarding filling the shape. It can be brought about by endeavoring to utilize the wrong resin type or by poor process settings, yet is most normally created by door blockages or too little of an entryway distance across, a typical issue because of too low weight or insufficient warmth. On the off chance that a higher soften file resin or expanded dissolve temperature doesn’t take care of a short shot issue, you may need to upgrade the runner framework to advance stream.
2 comments on “How to Avoid Common Injection Molding Defects”