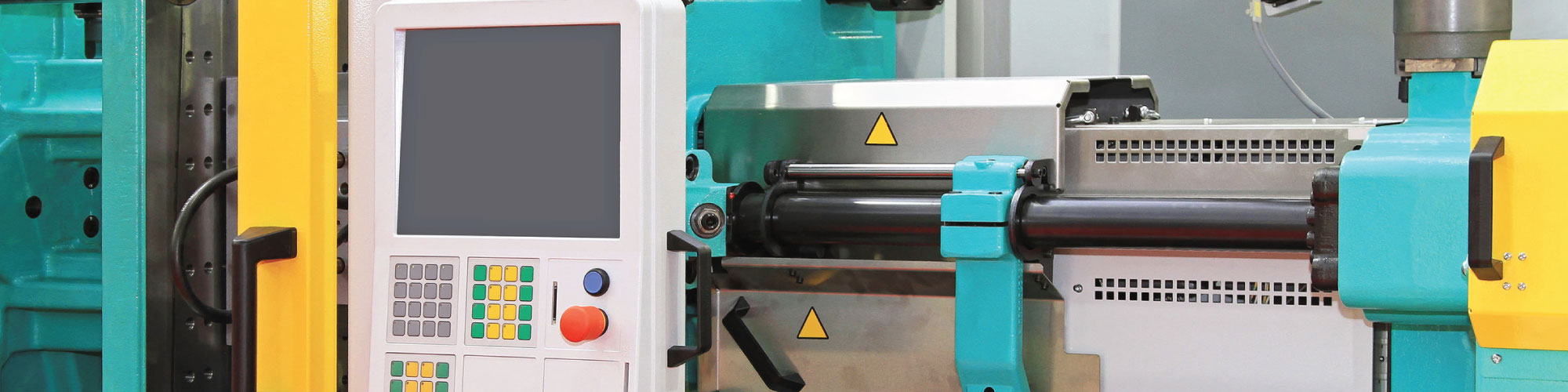
Top 5 Injection Molding Defects to Avoid
You need to recognize what sorts of value deformities to search for to ensure your item fulfills your client. We should take a gander at the assembling procedure and the infusion forming defects that generally influence these items.
Infusion shaping is a typical assembling process used to make segments made of metals, polymers, glasses, desserts and different materials. Pellets of material are liquefied and after that infused at high weight into a mold that will set to frame the coveted part. Infusion shaping is utilized to deliver things, for example, kitchen utensils, cultivate instruments, housings for hardware and some more.
Infusion shaping deformities
Deformities in infusion shaped items can by and large be ascribed to issues in one of the three ranges:
- The crude materials bolstered into the form
- The form, or
- The infusion forming process, (for example, the settings of the machine)
Here are five normal infusion shaping imperfections to keep an eye out for while reviewing infusion formed items, what the causes are and how you can dodge them:
1. Stream marks
Stream marks show up as a wavy pattern for the most part on smaller areas of the shaped segment. Liquid plastic, for instance, cools rapidly amid the infusion procedure and stream marks are clear when the infusion speed is too moderate. The plastic turns out to be somewhat strong and sticky while as yet topping off the form, causing the wave example to show up.
To evade this, the producer can expand the:
- Injection speed
- Nozzle breadth
- Cylinder temperature, and additionally
- Injection weight
For item review, stream imprints may be viewed as “minor” infusion forming absconds if unobtrusive and not on a noticeable piece of the thing. You should seriously think about a stream stamp to be a “noteworthy” imperfection on the off chance that it influences usefulness of your item or darkens a logo.
2. Short shot
A short shot is a fragmented segment which is caused by the stream solidifying off before the form is totally filled amid the infusion procedure. There are a couple of conceivable reasons why infusion may leave a void in the shape, for example,
- Flow limitations, more often than not because of mind boggling or solidified stream channels
- Hesitation amid infusion, or
- Inadequate venting causing a development of pneumatic force against the stream
You may see short shot in your plastic show as deficient compartments in plastic racks. A basic illustration is short or missing prongs on a plastic fork. Short shots are an average significant imperfection in infusion formed items.
Tending to short shots in assembling will rely upon the reason. On the off chance that the reason is identified with fill rate or wavering, raising the infusion weight, speed or temperature are conceivable cures. In the event that there is stream confinement, you may need to clear solidified stream channels or update the form. Also, insufficient venting is best tended to by including air vents close to the finish of the influenced channel(s).
3. Burn marks
Burn marks in the plastic show up as dark or dull red staining when the material consumes amid infusion. Normally considered a minor imperfection, a burn stamp amid the infusion procedure may be caused by at least one of the accompanying:
- Overheating because of caught air
- Excessive infusion speed, and
- Excessive dissolve temperature
In the event that you see consume stamps in your plastic parts, there are a couple of conceivable remedial moves to make in the assembling procedure. Shortening the process duration, bringing down the temperature as well as backing off the infusion speed may avert additionally consuming. Caught air can be settled by guaranteeing satisfactory gas vents and entryway sizes.
4. Streak
Streak is an abundance of filler material that can show up as a thin lip or distension at the edge of a part. This overabundance material shows up in light of the fact that material has streamed outside of the proposed stream channels between the plates. Streak is for the most part inconspicuous however may be viewed as a noteworthy imperfection if especially evident on an item. Some regular reasons for streak include:
- Poorly fitting or composed trim plates
- Insufficient clip drive, and
- Improper ventilation
- Improper blending of the masterbatch, the added substance utilized for shading material, or
- Impurities acquainted with the material amid the embellishment procedure infusion Molding Defects
Molds ought to be verified that their plates fit together appropriately and just enable material to stream in the channels. Clasping power may should be expanded, since this drive shields the material from streaming outside the stream channels. Finally, air vents may should be added to keep pneumatic stress from shaping and opposing the stream.
Unless the glimmer is significant to the point that tooling should be revised, trimming the segments is typically enough to guarantee these are not obvious on the completed item. On the off chance that inadmissible glimmer is showing up on your items, you can request that your provider ensure it’s trimmed before delivery.
5. Staining
Staining is an infusion shaping deformity that shows unspecified streaking or shading in an infusion formed item. Staining is ordinarily because of one of two causes:
In the event that the masterbatch is not uniformly blended, you may see a dash of shading at last item. What’s more, you can have polluting influences acquainted with a shape if the container, material nourish range or form plates of a machine are not cleaned legitimately before generation. To maintain a strategic distance from this issue, guarantee that the maker is appropriately cleaning the infusion shaping machine before delivering your things.
Contingent upon seriousness, staining could constitute either a minor or a noteworthy deformity. What’s more, there is no real way to evacuate this imperfection through revise of the completed item.
Conclusion
Since you have a thought of a portion of the normal infusion shaping deformities to pay special mind to, you’ll be in a superior position to survey the nature of your own items. You’re better arranged to survey a review report of your item or investigate the item yourself.
Recent Comments