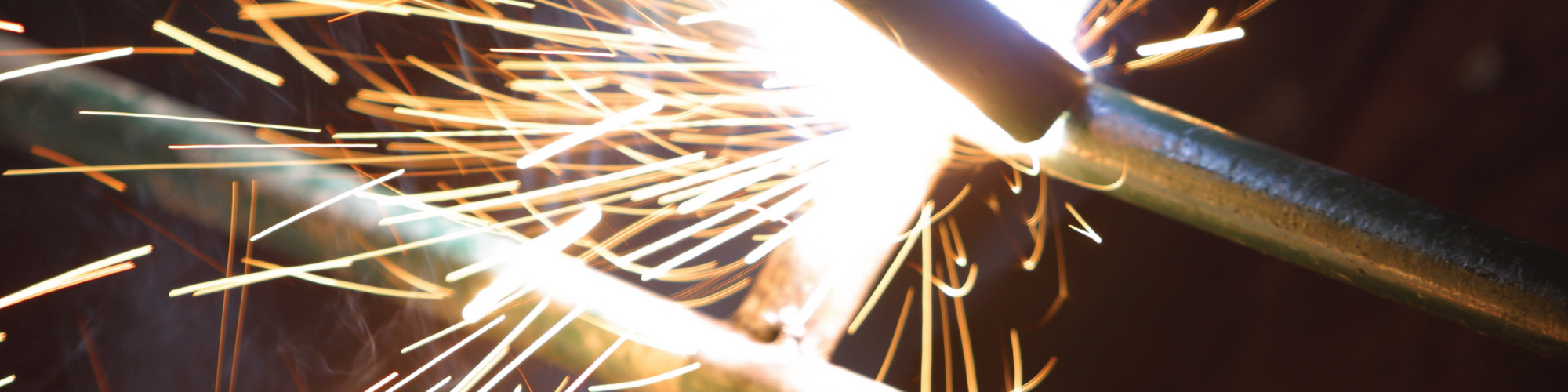
Designing for Manufacturing: Accuracy, Precision and Tolerance
With design projects and CAD programming now the default apparatuses for drawing product ideas, there is the threat of trusting that anything that can be designed can simply be made. Nonetheless, while exchanging a drawing from the ideal universe of the PC to the practical universe of the machine shop, certain fundamental contemplations apply that ought to give the designer pause. Knowing how to design an item for fabrication requires the comprehension of three key ideas: Accuracy, Precision and Tolerance.
Accuracy
Level of adjustment to a known standard or esteem.The standard for physical measurements is the meter, and its esteem is a widespread one in light of the separation that a light emission goes in a specific settled timeframe. Along these lines, precision is how much an estimation or development in space fits in with this known standard or one of its subordinates (regularly the millimeter or micron for metric estimations.)
In this way, when a machine apparatus is touted as being exceptionally precise, it implies that when the software engineer educates the machine to cut a bit of metal 40mm long, then the machine really does that. The more precise it is, the nearer it gets to precisely 40mm, with no blunder. There are numerous different variables required in getting precisely the 40mm cut that you’re searching for, yet simply recollect that we begin with a known esteem and exactness portrays how shut the machine gets to that esteem.
Precision
Repeatability of an estimation without producing irregular mistakes.Precision is the capacity of our machine instruments to rehash this 40mm cut, again and again, with no presented or irregular mistake. Exact machining, or exact workmanship, is a demonstration of controlling the procedure and not going amiss – paying little respect to whatever the estimation or process might be. This is regularly mistaken for exactness and to be sure the two terms are coolly utilized to some degree reciprocally however precision alludes more to repeatability.
In our feeling of precision, it likewise applies to the performance of the task, such as taking a cautious estimation or honing a cutter head or some other occupation in a machine shop whose performance eventually impacts the nature of the completed item.
Tolerance
Reasonable or unsurprising deviation from a standard.Each designer realizes that there is no such thing as ensured 100% exactness. There is just a settled upon standard. All machine instruments will have a level of free play or vibration in them – they should, or else they would be solidified, inactive pieces. The tolerance in this way indicates the deviation far from a referred to esteem, communicated as a “+/ – ” number. Along these lines, in the event that we have a machine instrument that claims a tolerance of “+/ – 1 mm”, this implies the apparatus will possibly present a deviation of one millimeter with each cut or pass. Could be an additional millimeter, or too short by a millimeter or some portion thereof.
This would be considered to a great degree poor performance, and no respectable machine instrument is that messy. Taken together, this implies exact instruments approach the standard, exact apparatuses are dependably precise again and again, and tolerances are controlled to inside a little, satisfactory level of changeability.
How does this influence Designing for Manufacturing?
As mentioned above, modern CAD programs are capable of generating 3D renders which are highly accurate, maybe too accurate. You will need to consider the following when designing your product:
- The accuracy and precision of the tools being used to make the product. In other words, what is the capability of the factory where your product is to be made? It’s good to know this in advance.
- The natural movement of the raw materials (metal and plastic of different types) in response to environmental conditions (temperature and humidity) and mechanical stress.
- Necessary allowance for movement. Draft angles are applied to parts which must be removed from a tooling mold, to make space for clearance without damaging the part. Other clearances must be allowed for pieces that have mechanical fittings: screws, axles, gears, etc.
- Kerf is the amount of material removed in the process of cutting. The computer model may not account for this lost material but the machinist must.
- More accurate is not necessarily better. Higher degrees of accuracy and precision require more effort, time and money for diminishing returns. Pursuing extreme accuracy in one feature of a design may compromise accuracy in another area. Many part features may need some free space to allow movement or room for thermal expansion/contraction between mating pieces of an assembly.
This web page is mostly a stroll-by means of for the entire information you needed about this and didn’t know who to ask. Glimpse here, and you’ll undoubtedly uncover it.