
A Guide into Sourcing Automotive Plastics
For a very long time, alloys have overwhelmed the general material substance of a car. Nonetheless, in the most recent decade, because of new regulations and fuel costs, there has been a noteworthy move to utilizing lighter weight materials, most commonly plastics or composites. This ascent in the car plastics is because of the business’ push to diminish the general mass of a vehicle, which is being driven by government controls and benchmarks (CAFE), and fuel costs.
An acquisition professional should always remember the following things before settling on a plastic injection molding crew. Not only do all of the following affect the overall pricing of the component, but equally as important, they affect the quality.
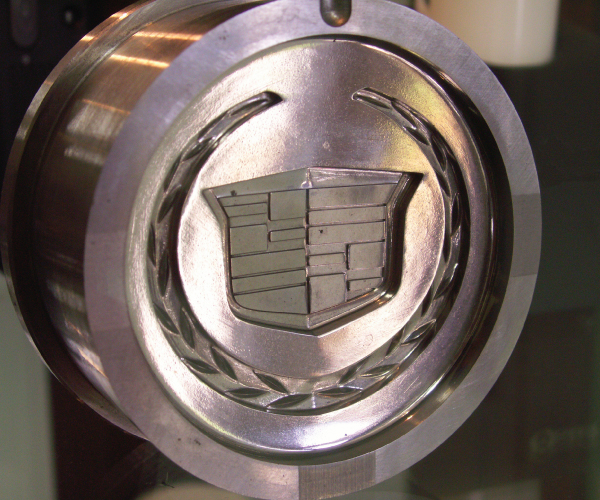
Key Considerations
Car plastics present one of a kind and valuable properties, for example, sturdiness, solidness, recycle capacity, heat stability, strength, protection, design adaptability, and light weight. The most widely recognized applications for plastics in autos are with the inside, outside and motor segments since they offer a lighter-weight choice, while expanding fuel effectiveness. Plastics likewise enhance the look or style, diminish noise and vibrations (NVH), keep in heat, and so on. Plastics offer a more reasonable way to deal with a more maintainable vehicle.
Process
To legitimately source a car plastic part, a plastic injection professional must consider and completely comprehend the procedure that the segment and application warrant. Many variables determine which process is worthy. These incorporate size, weight, shape, application, surface area, heat, stream, and so forth. The most well known plastic procedures for car applications, incorporate the accompanying:
Injection Molding
Injection molding is the most mainstream process utilized for car plastic segments. With this procedure, the plastic (in pellet frame) is put into a container which moves the plastic pellets into a warmed infusion unit, where it is pushed through a long chamber. The material is liquidized amid this procedure and solidifies in the wake of drying. For high-volume plastic segment programs, this is the prescribed procedure.
Thermoforming/Vacuum Forming
Thermoforming utilizes a plastic sheet, which is shaped with a form by applying air or through mechanical help. The pneumatic force utilized can be about zero psi, or a few hundred psi. At 14 psi, which is roughly proportional to air weight, the weight is made by emptying the space between the shape and the sheet. This is known as vacuum framing.
Blow Molding
At the point when the segment should be empty or have liquid move through, the blow shaping procedure is most useful for the application. A liquid tube is made with blow molding utilizing packed air, which explodes the tube and powers it to comply with the chilled form.
Pressure Molding
Pressure molding is the most well-known process utilized with thermosetting materials and is typically not utilized for thermoplastics. With this procedure, the material is crushed into its shape with the assistance of weight and warmth. At the point when the mold is shut and warmed, the material experiences a synthetic change that makes it solidify into the coveted shape. The temperature, weight, and time allotment used amid this procedure relies upon the coveted results.
Extrusion
The procedure of extrusion is normally used to make items, for example, film, ceaseless sheeting, tubes, profile shapes, poles, coat wire, fibers, cored, and cables. Similarly as with injection molding, dry plastic material is put into a container and bolstered into a long warming chamber. Toward the end of the chamber, the material is moved out of a little opening, or a die, in the state of the completed item. As the plastic leaves the die, it is put on a transport line where it is permitted to cool. Blowers are now and then used to help in this procedure, or the item might be submerged in water to enable it to cool.
Material
In light of the use of the part, its nearness to a heat source, area on the vehicle, and process, there are an assortment of elite plastics that are broadly utilized as a part of the car business, and a plastic injection molder must consider the attributes of every while sourcing a plastic segment. The most common materials for car plastics include: Polypropylene (PP), Polyurethane (PUR), Poly-Vinyl-Chloride (PVC), Acrylonitrile Butadiene Styrene (ABS), and Polyamide (PA, Nylon 6/6, Nylon 6).
Conclusion
The car plastics industry is situated to grow exponentially in the coming years. Understanding the above key aspects will guarantee trust in sourcing choices and offer organizations an upper hand in settling on future choices. Despite the fact that these thoughts are perhaps basic, there are numerous plastic injection professionals today settling on key choices without considering every single potential alternative with regards to plastic preparing and material determination. A true plastic injection molding expert will invest the energy it takes to completely comprehend plastic applications, volumes, procedures, and materials before sourcing to best plan their organizations can supply for your project.
Learn more about plastics and their qualties with this article! Looking for a plastic molder?