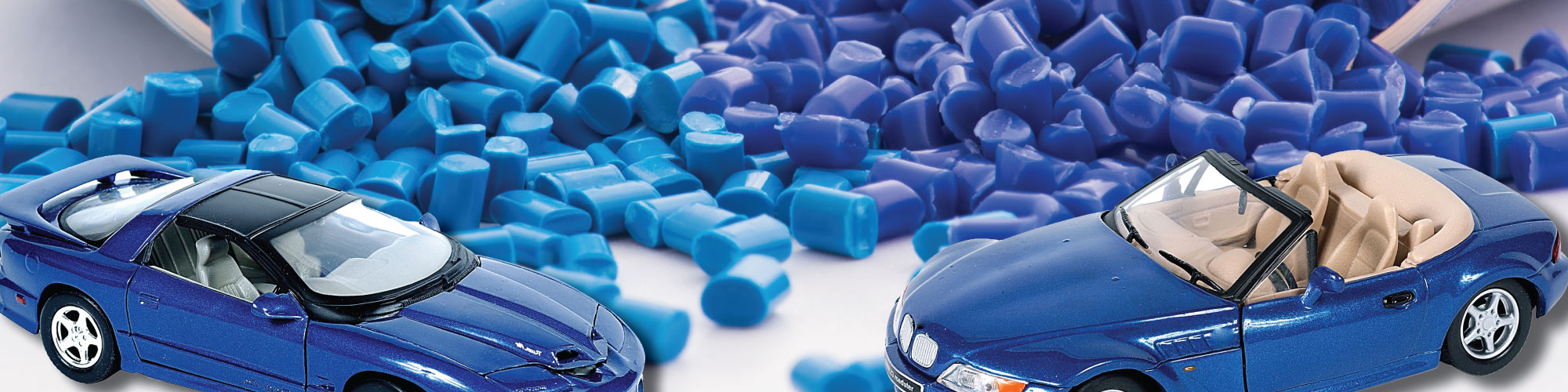
Inventor to Entrepreneur: Plastic Injection Molding
Plastic is a wonderful, versatile material that can be used for producing nearly anything! The great thing about plastic and injection molding is that it makes mass-production for products more accessible. It’s no longer necessary for every item you buy in the store to be meticulously handcrafted.
What makes plastic injection molding even better, is that entrepreneurs can come up with an endless amount of new ideas for products that will improve our daily lives. Everything from technology to basic toys have some plastic-molded parts. And while we don’t think of the injection molding process often, it’s part of our daily lives. Even the device you’re using to browse the Internet, has some plastic molded parts!
But if you, like the average person on the street, have no idea where to begin in making your product idea a reality through injection molding, there are some simple steps to take.
Is Your Idea Worth It?
The first, most important question to ask yourself before having a product mass-produced, is whether or not the product will truly be profitable. Unfortunately there’s no way to know for sure, and as with any new business venture, there will always be some risk involved.
But that shouldn’t stop you from doing your research.
When thinking about whether or not the product you want to make will sell, you can ask yourself some basic questions like:
- Does my idea solve a problem?
- Does my idea improve upon an existing product?
- Will there be a large enough market interested in buying my product?
- Can I explain the benefits of my product simple and succinctly?
- Can my product be manufactured at a realistic cost?
You’ll have to answer the first few questions for yourself by doing some market research. But the last one will require you to get quotes from product designers and plastic injection mold manufacturers.
Where to Start?
If you have a good idea that you believe will sell, your first challenge will be to get it on paper. Draw your design using some pen and paper. Don’t worry if you aren’t good at drawing, the important part is for your drawing to clearly show what you expect the finished product to be like.
You can also make some basic prototypes illustrating your idea using things like clay. Although it’s unlikely that a clay prototype would be functional, this will help designers understand what your product should look like in 3D. Apart from your clay prototype, you can also build a functional prototype using anything you can find around the house. This prototype will help you explain your idea more effectively.
Once you have proper designs and product examples, it’ can be a good time to venture into having it made in plastic. When you start out, getting your idea 3D printed can be an excellent way to make a realistic prototype of the end product.
3D printing is a wonderful technology for producing small amounts of plastic parts without the upfront investment of having a plastic injection mold made. For this reason, some products never go further than the 3D printing stage. An example of an innovative for 3D printing is in the manufacturing of prosthetics for amputees. Because every amputee has very specialized individual needs, 3D printing is now used to manufacture low-cost, custom-made prosthetics.
However, most products have to be mass-produced in order to be profitable, so for the purpose of your product design, you’re likely to use 3D printing only during the prototyping phase of design.
Once you’ve got a basic, 3D printed prototype of your final product, you’re ready to take the idea further. If there’s anywhere you were hoping to pitch your product idea, the prototype is sure to come in very handy!
Let’s Talk CAD Designs
This is where you hand your ideas over to the professionals. Computer-aided design – or CAD, for short – is a process where professional designers take your idea to the next level.
CAD designers know more about the injection molding process and the manufacturing of plastics products in general, so their designs will usually be made considering different aspect of the manufacturing process. This is essential for successful product design, seeing as a plastic injection mold will have to be designed and made specifically to produce parts for your product. The professional product designers will draw the final product design, not only thinking about the functionality of your product, but also how the molds producing parts for your product will function.
Some of the things a professional CAD designer will keep in mind while designing the final product include:
- What material will be used to make each part of the final product?
- How easily can each part of the final product be molded?
- Where should the gates be placed on the mold to ensure the part has no molding defects?
Chances are, your designer will take an example of their design to a plastic injection mold manufacturer in order to decide how the molds should function. Plastic injection mold design and quality in the manufacturing of the mold itself will play a huge role in the quality of your final product.
If the gates feeding molten plastic into the mold aren’t placed correctly, for instance, the plastic might not fill the whole mold cavity and your parts could all end up being defective.
For this reason, your mold designer and manufacturer will be just as important in getting your product idea on the shelf as your designer.
At Quality Mold Shop, we pride ourselves in producing precision molds for any industry. We’ve successfully designed and maintained injection molds for the technology, medicine and the automotive industries. Talk to us about mold design, maintenance and manufacturing.
2 comments on “Inventor to Entrepreneur: Plastic Injection Molding”