
Types of Plastic Blow and Injection Molding Part 2
Injection stretch blow molding consolidates the injection molding and blow molding processes. The plastic is first formed into a strong preform, to make a threaded container neck. Once the preform cools it is encouraged into an extend blow form machine. The preform is then warmed utilizing an infrared radiator and blown into a plastic jug with constrained compacted air.
Injection molding and blow molding are two predominant procedures in plastic molding. Items made through these procedures are utilized as a part of an extensive variety of businesses, for example, car, food perp, hardware, medical gear, water system, dental, guns, energy and environment enterprises.
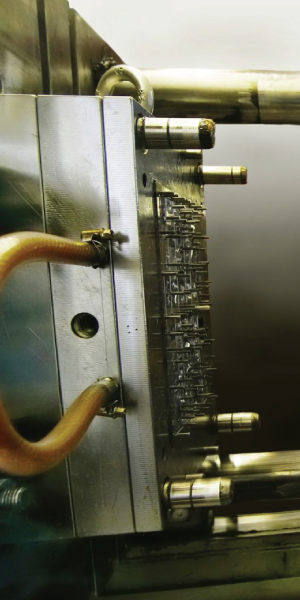
The Blow Molding Process
Amid the blow molding process, the resin plastic material is molded into an empty tube with one open end called a parison. The parison is squeezed into a cooled metal form and packed air is blown into the parison. At the point when the shaped plastic cools and solidifies, the metal form opens and removes the item.
There are three kinds of blow forming forms:
Injection Blow Molding
In injection blow molding, a blow or center pole is utilized all through the procedure. To start with a parison is infused into a part form hole around the bar. The parison that is shaped seems to be like a test tube. The center bar transfers the parison to the blow mold machine where constrained air makes the last shape. The bar at that point exchanges and expels the completed item from the machine.
Extrusion Blow Molding
Extrusion blow molding can be constant or discontinuous. In consistent expulsion blow molding, a parison will be continually moved into the mold and each frame will be cut off with a cutting edge as it forms. Intermittent Extrusion blow molding ousts each new plastic from the metal form when it is cooled and the parison is put into the mold after the previous parison is removed.
Extrusion blow molds are for the most part significantly less costly than infusion blow molds and can be created in a considerably shorter timeframe. Extrusion blow molding is suitable for short runs.
Injection Stretch Blow Molding
Injection stretch blow molding consolidates the infusion molding and blow molding procedures. The plastic is first shaped into a strong preform, to make a threaded container neck.
Once the preform cools it is put into a stretch blow molding machine. The preform is then warmed utilizing an infrared warmer and blown into a plastic container with constrained packed air.
What Molding Processes Does Your Product Require?
What sort of assembling process is appropriate for your next venture? Our architects have many years of experience and comprehend what kind of material and form is appropriate for you. Get in touch with us to examine your new plastic design and we will walk you through the assembling procedure that is best for your task needs.
Recent Comments