
Are You Ready to Produce Consumer Goods in 2018
What are consumer goods? Consumer goods are products that are purchased for direct consumption to fulfill a human need or want. Consumer goods are the end results of production and manufacturing and are what a consumer will see on the store shelf. Another name for consumer goods, which is more common, is final goods. There are various types of consumer goods and multiple different ways to create them. Quality Mold Shop, founded in 1976 by Douglas Boles, is a business that is family owned, and they are striving to provide the best quality of plastic injection molds. The molds are later used to produce top-quality consumer goods.
Main Types of Consumer Goods
There are various types of consumer goods: durable goods, nondurable goods, and services. Durable goods are the ones that have a long lifespan and are used over time. The typical lifespan is about 3 years or more. Some examples would be clothes, toys, and jewelry. Nondurable goods are goods that are consumed in less than 3 years and have a short lifespan such examples would be food items and drinks. The service goods are things such as getting a haircut or repairs.
Mold Building For Consumer Goods
There are many different ways to produce consumer goods. One of the ways to produce the good is using injection molds. Quality Mold Shop is able to design and produce the injection molds in mass quantities that are strong enough to withstand the assembly line. To create the injection molds, they use top-notch manufacturing equipment, computers, and software along with the best-experienced personnel. Their manufacturing facilities are located in McMinnville, TN. The mold making process starts off like this:
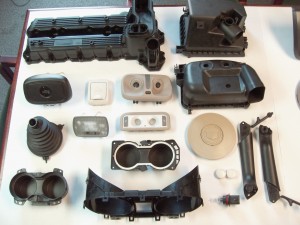
- The design of the product is sent over to the injection mold design department. There, the designers do a complete cost analysis.
- If the project was approved, then the designers assign certain personnel to review the product information such as the product’s structure, mold structure, cooling system, runner, slag, and venting.
- Whenever the review is complete, injection mold designers start using 3D drawings and 3D parts to sketch out the layout. After it has been approved, injection mold makers evaluate and order all the materials used to create the mold.
- Technicians do locksmith work to it. After the heating process, the mold maker must detect its sturdiness.
- Before putting together the mold, the mold maker needs to complete an inspection. The inspection is to make sure everything is in good condition, cleaned, and goes through an anti-rust treatment.
- In the last step, the plastic molds are tested out. Once they go through that process, they are stored and used whenever needed.
Advantages of Injection Molding
There are many advantages to having plastic injection molding.
- Saving Manufacturing Cost: The injection molding is an automated process. Majority of the assembling is done with the aid of technology such as machines and robotics. This cuts down on hiring people to work; therefore, cutting down on labor costs.
- High Efficiency: The injection molds are customized and created specifically for a certain product, so the number of mistakes is cut down. The actual molding process and drying process are super quick, so this allows for high production rate.
- Smooth and Sleek Appearance: Unlike other materials, plastic injection mold products come out smooth and shiny. They do not require finishing, and because of this, it saves you time and extra work.
Recent Comments