
Injection Molding Equipment
In the present assembling condition, plastics are being utilized to make everything from car body parts to human body parts. Every application requires an uncommon assembling process that can mold the part with all of its details. This article gives a short outline of the diverse sorts of equipment, specifically machines and their advantages and applications.
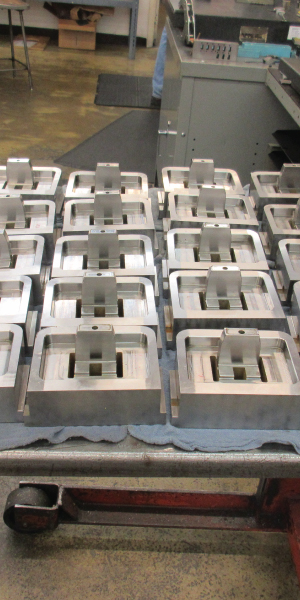
Blow Molding – appropriate for empty items, similar to bottles
The procedure takes after the advances found in glass blowing. A parison (warmed plastic mass, normally a tube) is swelled via air. The air pushes the plastic against the form to frame the coveted shape. Once cooled, the plastic is launched out.
The blow molding process is intended to make high volume, one-piece empty items. On the off chance that you have to make heaps of jugs, this is the procedure for you. Blow molding makes exceptionally uniform, thin walled holders.
Compression Molding – appropriate for bigger articles like car parts
The name of this molding strategy says everything. A warmed plastic material is put in a warmed form and is then compressed into shape. The plastic can be in mass however frequently comes in sheets. The warming procedure, called curing, guarantees the final part will keep up its strength. As with other molding techniques, once the part has been formed, it is then expelled from the mold. On the off chance that sheeting plastic material is utilized, the material is first trimmed in the shape before the part is evacuated.
Extrusion Molding– appropriate for long empty framed applications like tubing, pipes and straws
While different types of molding utilize extrusion to get the plastic resin into a mold, this procedure expels the liquefied plastic specifically into a die. The die shape, not a mold, decides the state of the last item. The expelled “tubing” is cooled and can be cut or moved for shipment.
Injection Molding – appropriate for fantastic, high-volume part producing
Injection Molding is by a long shot the most flexible of all injection molding methods. The presses used in this process vary in size and are rated based on pressure or tonnage. Larger machines can injection mold car parts. Smaller machines can produce very precise plastic parts for surgical applications. In addition, there are many types of plastic resins and additives that can be used in the injection molding process, increasing its flexibility for designers and engineers.
Conclusion
Each sort of molding has its qualities and shortcomings. Designers and specialists need to comprehend these distinctions and the creation alternatives accessible between all the injection molding equipment. The molding company who consults on a specific project should be able to provide additional insights into the applications and materials that are best suited to an individual project. If you’re in the market to get your part made, Quality Mold Shop is ready to help. Give us a call today.
Recent Comments