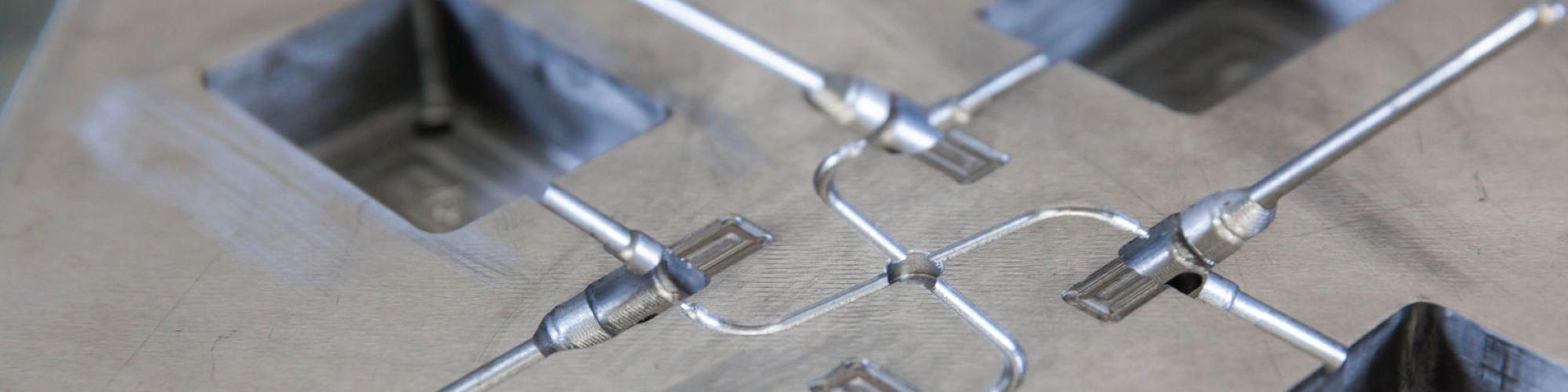
Types of Plastic Blow and Injection Molding Part 1
Every plastic part requires a particular assembling process which can be quite unique one item to another. Injection molding is utilized to fabricate solid parts while blow forming is utilized to make plastic items with empty regions, for example, jugs and bottles.
Injection molding and blow forming are two main procedures in plastic assembling. Items made through these procedures are utilized as a part of an extensive variety of ventures, for example, car, food industries, gadgets, medical equipment, water systems, dental, guns, energy and environment enterprises.
To enable you to better comprehend the diverse assembling strategies accessible for your venture, we have put together a two section arrangement of the primary kinds of injection and blow molding methods used by plastics manufacturers.
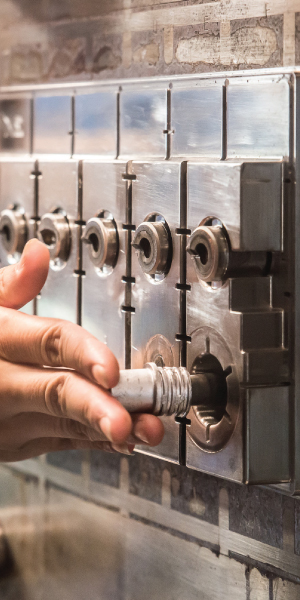
The Injection Molding Process
Injection molding is utilized to fabricate higher volume amounts of plastic items extending in estimates from huge parts to little segments requiring smaller scale exactness precision.
There are many kinds of assembling strategies ordered under injection molding, for example, thermoplastic injection molding, over molding, insert molding, cold runner molding and hot runner molding.
Thermoplastic Injection Molding
Thermoplastic injection molding utilizes thermoplastic polymer, which means it changes to a fluid state when warmed. Not at all like thermoset plastics that cool into perpetual strong, thermoplastics can be reheated to a liquid after cooling into a solid.
Overmolding
Overmolding, or two shot molding, is a procedure that covers an injection mold over another substance, for example, metal, to enhance the execution or strength of an item. An elastic like compound, called thermoplastic elastomer (TPE), is a utilized overmold material. A case of a TPE overmold application is the handles on a toothbrush. Overmolds can likewise be utilized to seal items with parts produced using a few injection molds.
Insert Molding
Like overmolding, insert molding is an injection molding process that joins at least two parts into a solitary completed item. Insert injection molding embeds a part into the injection mold and plastic material is filled around the insert. Inserts can add quality to an item and dispose of the requirement for extra parts to decrease the item weight.
Cold Runner Injection Molding
Cold runner molds utilize a sprue to fill the runners that infuse plastic resin into the mold. In 2 plate molds, the runner framework and parts are appended, and a discharge framework might be utilized to isolate the part from the mold. The cold runner can decrease waste by reusing and regrinding the material, yet this can likewise build the full process duration. Cold runner frameworks can be utilized for a wide assortment of polymers and can take into consideration simple shading changes.
Hot Runner Molds
Hot runner molds utilize a system to melt softened plastics and after that send the material through a door to fill the mold depression. The two principle sorts of hot runner molds are eternally heated and inside heated. The externally warmed molds can be utilized with polymer that is less touchy to warm while inside warmed hot runner molds take into consideration better control of material stream.
Since hot runner molding does not require the utilization of runners, potential waste material is reduced and the recycling and regrind and process of virgin plastic does not impact the total run cycle time.
In the next part we will go over the blow molding processes in plastic injection molding. If you have any questions feel free to give Quality Mold Shop a call or comment down below. Our engineers have decades of experience and understand what type of material and mold is right for you. Contact us to discuss your new plastic design or product idea today and we will walk you through the manufacturing process that is best for your project needs.